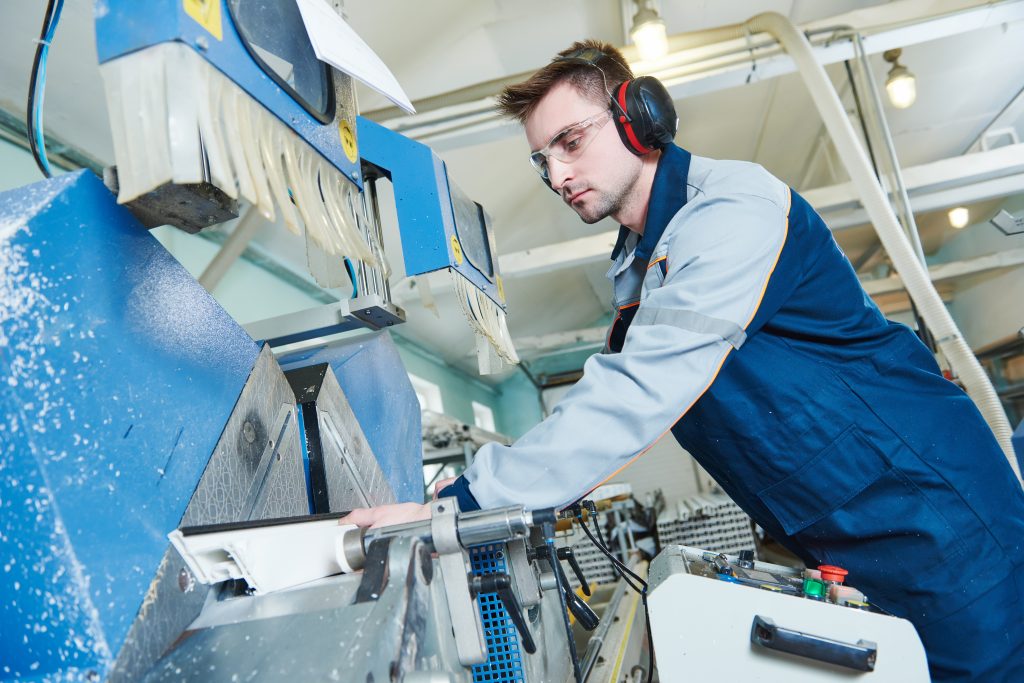
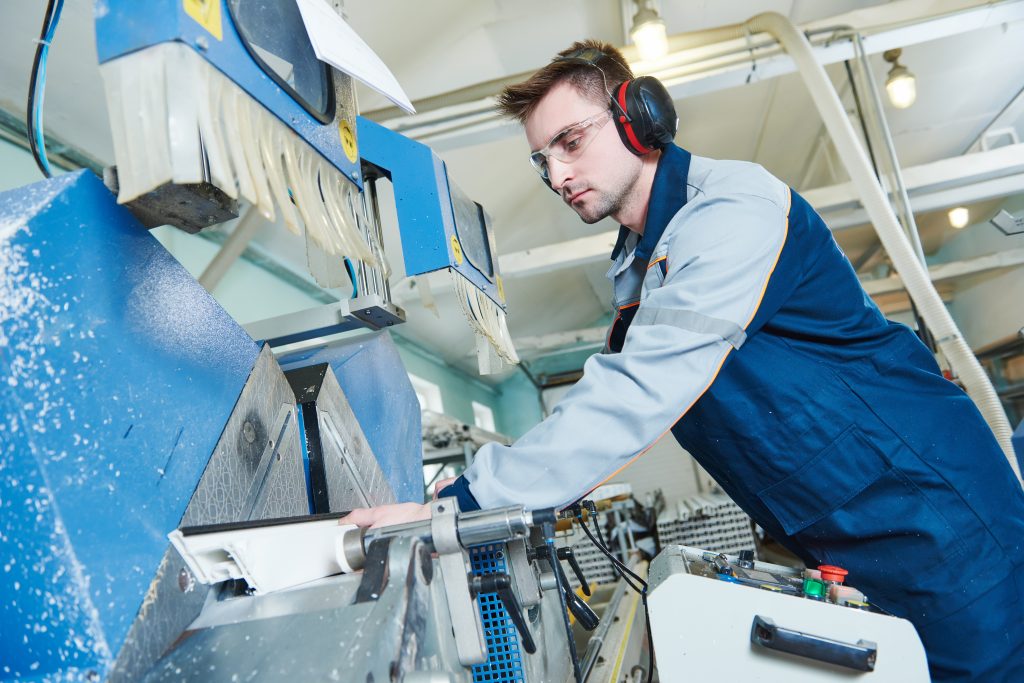
The Comprehensive Guide to Conducting an Ergonomics Assessment
Ergonomics assessments are vital in ensuring that workplaces are optimised for the health and productivity of employees. By systematically analysing work environments, companies can identify potential risks and implement solutions to improve overall ergonomic standards. This blog post will walk you through the essential steps involved in conducting an effective ergonomics assessment, focusing on Task Load surveys, Contextual Enquiries, Ergonomics Risk Assessments, and Detailed Reporting. Additionally, it will highlight how UK companies should adhere to specific regulations and standards, as well as best practices in ergonomics.
1. Task Load Survey: Measuring and Benchmarking
The first step in an ergonomics assessment is to conduct a Task Load survey. This survey provides a detailed understanding of the workload across different departments and the company as a whole. The survey includes:
- Quantitative Data Collection: Employees rate their perceived task load on various dimensions such as mental demand, physical demand, temporal demand, performance, effort, and frustration.
- Task Load Score: Each department and the entire company receive a Task Load score, allowing for benchmarking against other organizations. This score helps to identify areas where employees might be overburdened or underutilized.
- Thematic Analysis of Open Comments: In addition to quantitative data, the survey includes open-ended questions. A thematic analysis of these comments can reveal key themes and insights into factors impacting ergonomic risk. For example, employees might highlight issues such as inadequate equipment, poor workstation layout, or excessive repetitive tasks.
This comprehensive survey sets the foundation for identifying high-risk areas and prioritising interventions.
2. Contextual Enquiry: Understanding the Day in the Life of Employees
To gain a deeper understanding of the employee experience, a contextual enquiry is conducted using theoretical sampling. This involves:
- Selection of Participants: Users should be selected based on level of insights. Try to go for extreme users as this will highlight poor design issues.
- Observation and Interviews: Ergonomists spend time observing employees during their typical workday and conduct interviews to understand their tasks, challenges, and work environment.
- Detailed Documentation: Notes, photographs, and videos are collected to capture the nuances of each employee’s work experience.
The contextual enquiry provides qualitative insights that complement the quantitative data from the Task Load survey, offering a holistic view of the work environment.
3. Ergonomics Risk Assessment: Applying Standardized Tools
The next step involves conducting an ergonomics risk assessment using established tools such as REBA (Rapid Entire Body Assessment), RULA (Rapid Upper Limb Assessment), ART (Assessment of Repetitive Tasks), MAC (Manual Handling Assessment Charts), and RAPP (Risk Assessment of Pushing and Pulling).
- REBA: Assesses the entire body’s posture, force, and type of movement, identifying high-risk tasks that might lead to musculoskeletal disorders.
- RULA: Focuses on the upper limbs, evaluating the risk associated with repetitive movements and awkward postures.
- ART: Evaluates the risk of repetitive tasks, considering factors like frequency, force, and posture.
- MAC: Assesses the risks involved in manual handling tasks, such as lifting, carrying, and lowering loads.
- RAPP: Identifies risks related to pushing and pulling tasks, including the weight and distance of movements.
These tools provide a structured approach to identifying ergonomic risks, allowing for precise interventions.
Adhering to Regulations and Standards
For UK companies, it’s essential to align ergonomics assessments with relevant regulations and standards to ensure compliance and enhance workplace safety:
- Manual Handling Regulations: For manual handling tasks, companies should work alongside the Manual Handling Operations Regulations 1992 (MHOR). This involves conducting risk assessments, providing adequate training, and implementing appropriate control measures to minimize the risks associated with manual handling.
- Upper Limb Disorder Guidance: Companies should follow guidance from the Health and Safety Executive (HSE) for managing upper limb disorders (ULDs). The HSE provides comprehensive resources and guidelines for identifying, assessing, and controlling risks associated with ULDs. For more information, visit the HSE Upper Limb Disorders page.
- ISO Standards: For broader ergonomic considerations, companies should refer to standards from ISO TC 159, which provides guidelines on ergonomic principles. ISO 14738, for example, offers guidance on workplace design, including workstation layout, equipment design, and environmental conditions.
Best Practices in Ergonomics
In addition to the structured assessment process, incorporating the following best practices can further enhance ergonomic outcomes:
- Ergonomics Training and Education: Provide regular training sessions for employees on ergonomic principles, proper posture, and the use of ergonomic equipment. Educated employees are more likely to adopt healthy work habits.
- Involve Employees in Ergonomics Solutions: Engage employees in identifying ergonomic issues and developing solutions. Their firsthand experience and insights can lead to more practical and effective interventions.
- Continuous Monitoring and Feedback: Establish a system for ongoing monitoring of ergonomic conditions and soliciting employee feedback. This can include regular check-ins, surveys, and follow-up assessments to ensure that implemented solutions remain effective.
- Encourage Movement and Breaks: Promote regular breaks and encourage employees to move and stretch throughout the day. This can help mitigate the risks associated with prolonged static postures and repetitive tasks.
- Ergonomics Integration in Workplace Design: Consider ergonomics in the initial design and layout of workspaces. Collaborate with architects and designers to create environments that support ergonomic principles from the outset.
4. Detailed Report: Setting Out Findings and Recommendations
The final step is to compile a detailed report that outlines the findings from the Task Load survey, contextual enquiry, and ergonomics risk assessment. The report should include:
- Executive Summary: A high-level overview of key findings and recommendations.
- Detailed Analysis: Comprehensive data and insights from the Task Load survey, including quantitative scores and thematic analysis.
- Contextual Insights: Qualitative findings from the contextual enquiry, highlighting specific issues and employee feedback.
- Risk Assessment Results: Detailed results from the ergonomics risk assessment tools, identifying high-risk tasks and areas.
- Regulatory Compliance: An overview of how the findings align with relevant UK regulations and ISO standards.
- Recommendations: Specific, actionable recommendations to address identified risks and improve ergonomic conditions. This might include changes to workstation design, task redesign, introduction of ergonomic tools, or employee training programs.
By following these steps, adhering to relevant regulations and standards, and incorporating best practices, companies can ensure a thorough and effective ergonomics assessment. This approach leads to a healthier and more productive workplace, with regular follow-up assessments to track the impact of interventions and ensure continuous improvement in ergonomic standards.
Need help with your MSD/RSI/Ergonomic Risk Assessment and overall MSD prevention and ergonomics improvement process? Contact Morgan Maxwell today to speak with a Chartered Ergonomist. We can help you identify the right ergonomic risk assessment, checklist, tool, or evaluation for the job. If you’re unsure whether you need a Chartered Ergonomist’s expertise, see our blog post first: What is a Chartered Ergonomist?, and drop us a line with any questions.